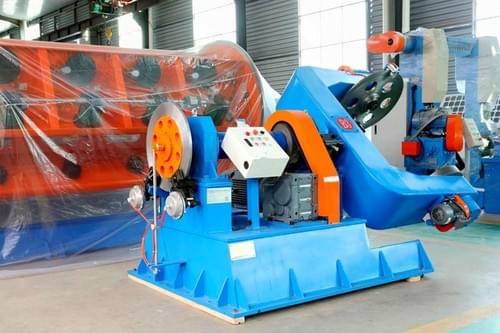
1 x 2000 + 4 X 1600—PN2500 Drum twister Laying-up Machine
Model: 4xPN1600+1X2500 +2500
Payment Terms: T/T, L/C, D/P, Etc.
Delivery Time:140 Days
Place Of Origin: China
Port Of Loading:China
Shipping:By Sea
HS Code:8479400000
Container Load:4*40HQ+3*40OT+4*40FR
Warranty Period:12 Months
1 x 2000 + 4 X 1600—PN2500 Drum twister Laying-up Machine.
1. Use:
Mainly used for twisted and lay-up cable of large section and large length power cable
2.Main Component ;
2.1 Fork type pay-off frame: 1xPN2000+PN1600x4 set
2.3 Rotation die holder : 1 set
2.4 meter counter: 1 set
2.6 Caterpillar pneumatic traction device ; TQD4000 1 set
2.7 Double head Taping device: RB500 1 set
2.8 Double head steel belt armouring machine : KRB800 1 set
2.9 Drum head: PN2500 1 set
2.10 Steel wire armouring machine: 86 wire 1 set
2.11 Filling frame: 2 set
2.12 Safety fence: 1 set
2.13 Electrical control system: 1 set
3.The main technical parameters:
3.1Fork type pay-off frame:4Set
3.1.1The forked pay-off is driven separately by a 15KW motor. The load reel is in the form of a shaftless, which is tightened by two 0.55 kW motor drive turbines. The tension control is a pneumatic disc type, and the tension level can be adjusted by the pneumatic pressure regulating device without stopping the tension. The brake system is a pneumatic disc brake that is braked by two sets of pneumatic brake calipers. The 4 fork-type pay-offs are equipped with independent operation control cabinets, which can perform forward rotation, reverse rotation, jog, emergency stop, and tightening of the reel. Each of the 5 pay-offs is equipped with an adjustable two-way two-way guide roller crossover frame. The overall operation of the 4 sets of discharge lines is controlled by the touch screen operation PLC, which can be synchronized with the drum head or fixed. The loading and unloading of the reel is assisted by the hoisting machinery in the demand side.
3.1.2 Max rotation speed:45r/min
3.1.3 Max load weight: 5T
3.1.4 Reel size: φ1600mmx1180mmxφ80mm.
3.1.5 Structure form: Fork cantilever structure.
3.2 central pay-off frame;
3.1 Fork type pay off is driven by 22KW motor separately,. The hanging plate is of shaftless type, which is tightly loosened by two 0.55kw motor driven turbine boxes. The tension control is pneumatic butterfly type, and the tension can be adjusted by the pneumatic pressure regulating device without stopping. The brake system is a pneumatic butterfly brake, which is braked by two groups of pneumatic brake calipers. Equipped with independent operation control cabinet, it can carry out forward rotation, reverse rotation, inching, emergency stop, tightening and loosening of wire coil. Both of them are equipped with adjustable two horizontal and two vertical guide rollers. The operation is coordinated and controlled by the touch screen operation PLC, which can run synchronously with the winch head or be fixed. The wire tray loading and unloading shall be completed with the assistance of the hoisting machinery in the buyer's yard
3.2.2 Max rotation speed:45r/min
3.2.3 Max load weight:8T
3.2.4 Reel size:φ2000mmx1500mmxφ125mm
3.2.5 Structure form:Fork cantilever structure
3.3 rotation die holder;
120mm Passive rotary mold base consists of two rotatable mold bases, both mold bases are quick change mold bases.
3.4 Mechanic meter counter:
3.3.1 Pressing the wire by two belts increases friction and improves metering accuracy.
3.3.2 Equipped with 5-digit mechanical counter.
3.3.3 Equipped with multi-point electronic counter with electronic meter counter function.
3.4 Caterpillar pneumatic traction device
3.4.1 It consists of two sets of reinforced tracks that are pressed against the cable by ball bearing rollers mounted on each cylinder. The opening and closing of the belt is realized by the control of the single operation cabinet, which can realize the forward and reverse running of the tractor, jog, emergency stop and tightening of the track. It consists of 10 pairs of cylinders to achieve compression of the cable. Each track is equipped with a set of air springs to achieve the tension of the track. Suitable for cables of 120 mm diameter. The inlet end of the tractor is equipped with adjustable two horizontal and two vertical guide rollers. The traction is driven by a 30KW motor through the gear box to drive the track to meet the pulling force required for traction. The traction main body transmission and the take-up ground axis linkage are driven by 55KW motor, the rotation direction and the rotation speed are the same as the rotation receiving line, and the touch screen operation PLC unified coordination control/
3.4.2 Max traction force:4000KG
3.4.3 Brake form:Pneumatic disk type
3.4.4 Max through diameter: φ120
3.4.5 Max rotation speed:45r/min
3.4.6 Traction pitch range: 300mm-5000mm
3.5.7Power :45kw
3.5 steel belt taping machine:
3.5.1 Driven by a single 11KW motor, it is mainly used for the winding of steel strips on the outer layer of the cable. The locking mechanism of the tape reel has a locking mechanism. The body is run through a polished chrome-plated guide roller, laid on the cable, and connected at the steel strip and cable. Mold bases are provided on both sides to maintain the stability of the cable during winding of the steel strip. The inlet end is equipped with two adjustable two horizontal guide rollers. It has the function of stopping the belt and finishing the belt (the steel belt is used up). With a little movement, the emergency stop is reversed, the button. The winding speed pitch is uniformly coordinated and controlled by the touch screen PLC. Equipped with an integrated safety shield and open parking.
3.5.2 Brake form: Pneumatic disk
3.5.3 Max through line diameter:φ120
3.5.4 Steel belt reel outer diameter: φ800mm
3.5.5 Taping belt width range: 15mm-80mm
3.5.6 Taping belt twisting form:Tangential
3.5.7Taping belt reel quantity:2 reels
3.6 Double head taping device:
3.6.1 Driven by a separate 7.5KW motor. It is mainly used for the laying of the outer layer of the cable such as non-woven fabric and PVC. The locking mechanism of the belt and the clamping plate has a locking mechanism. The body is run through a polished chrome-plated guide roller, which is laid around the cable and is linked with the cable. There are molds on both sides of the point to maintain the stability of the cable during winding of the tape. The inlet end is equipped with two adjustable two horizontal guide rollers. With the broken belt and the end belt (wrap around the belt) parking function. With a little movement, the emergency stop is reversed, the button. The winding speed pitch is uniformly coordinated and controlled by the touch screen PLC. Equipped with integrated safety guard and open parking
3.6.2Brake form:Pneumatic disk
3.6.3 Max through line diameter:φ120
3.6.4Taping taking reel outer diameter:Φ600mm
3.6.5 Taping belt width range:15mm-60mm
3.6.6T aping belt twisting form:Tangential
3.6.7Taping belt reel quantity:2 reels
3.7 Drum head;
3.7.1 The drum head is driven by a 55KW motor in conjunction with the tractor through the ground shaft. With independent control cabinet, it can carry out operations such as forward and reverse, jog, emergency stop, and tightening of the reel. The traverse device is mounted on the disc winch and driven by the motor through the deceleration device, and is controlled by the touch screen PLC. The upper plate is a shaftless electric tightening, which is driven by two 0.55KW motors to tighten the coil. The winding motor is installed on two fork arms of two 4KW motors. The take-up function is realized by the gear box to drive the coil. Here, the double power take-up line can make the take-up process and the machine run more smoothly. Take-up is evenly spaced. The speed of the whole machine, the strength of the winding line, the speed of the traverse are all coordinated and controlled by the Siemens touch screen PLC. The loading and unloading of the drum head coil is completed by the equipment in the workshop.
3.7.2 Max rotation speed:45r/min
3.7.3 Max load weight:10 T
3.7.4 Traverse pitch:15mm~150mm
3.7.5 Take-up bobbin size:PN2500mm
3.7.6 Take-up frame structure:Forked roller structure
3.7.7 Brake form:Pneumatic disk。
3.8 Steel wire armouring machine:
The unit has an 80-wire steel wire armouring function that enables steel wire laying during the lay-up process.
3.9 Electrical control system:
3.9.1 The operation and operation of the entire unit is completed by an independent master control cabinet, and separate units are provided for easy operation. The total control cabinet is controlled by the touch screen operation PLC to coordinate and control various parameter settings of each unit in the cable forming process, and can display the running speed and the running parameters of each unit in real time, so as to facilitate timely modification and adjustment of the operating parameters of each unit.
3.9.2 Safety protection: This machine has a number of safety protections, which can provide corresponding protection measures in case of failure or failure to meet the normal operation of the equipment, and timely display the fault point on the screen of the main control cabinet, so that the operator can make timely Accurate judgment and effective treatment plan
3.9.3 Horizontal protection for each pay-off and take-up fork
3.9.4 Fault alarm for all motors of the entire unit
3.9.5Traverse Overtravel protection
3.9.6 Air pressure undervoltage protection
3.9.7 Each unit power protection
3.9.8 Taping break and finishing protection.