How to Making Outdoor Optical Fiber Composite Ground Wire (OPGW)?
Optical Fiber Composite Ground Wire (OPGW) is a dual-function cable used in high-voltage power transmission lines. It serves as:
A ground wire (for lightning protection and electrical grounding).
A fiber optic communication cable (for data transmission).
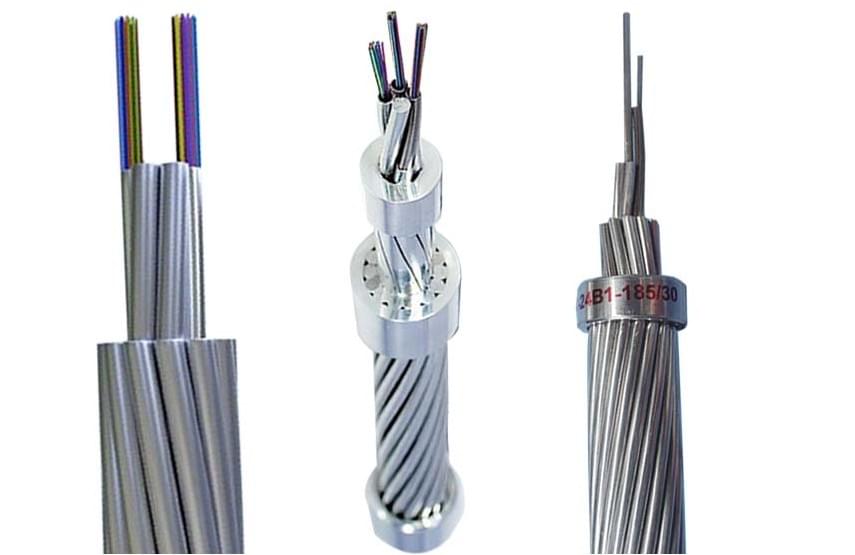
1. Design & Material Selection
Before production, engineers must determine:
Voltage level (e.g., 110kV, 220kV, 500kV)
Mechanical strength (tensile load, wind/ice resistance)
Fiber count (typically 12, 24, 48, or 96 fibers)
Conductor material (usually aluminum-clad steel or all-aluminum alloy)
2. Manufacturing Process
Step 1: Fiber Unit Preparation
Stainless steel loose tube production line SSLT making machine
Optical fibers are placed inside a loose tube (stainless steel or aluminum).
The tube is filled with water-blocking gel to prevent moisture damage.
Fibers are color-coded for identification.
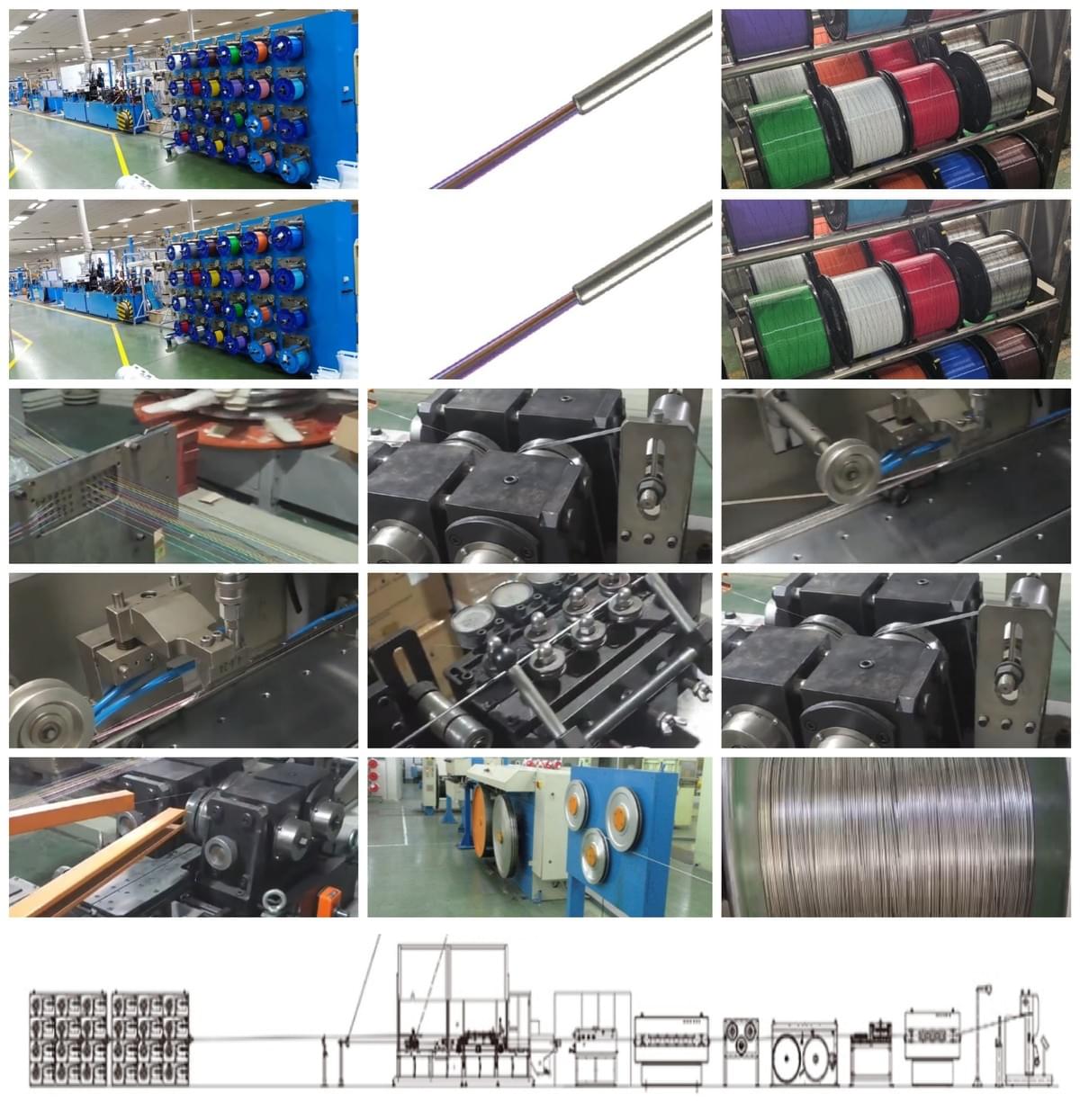
Step 2: Stranding the Outer Conductors
The central fiber tube is surrounded by aluminum or steel wires in a helical pattern.
Common stranding methods:
Single-layer stranding (for smaller OPGW)
Double-layer stranding (for higher mechanical strength)
The most suitable machine here is the “Planetary stranding machine",
The 500 model is faster and cheaper than the 630 model.
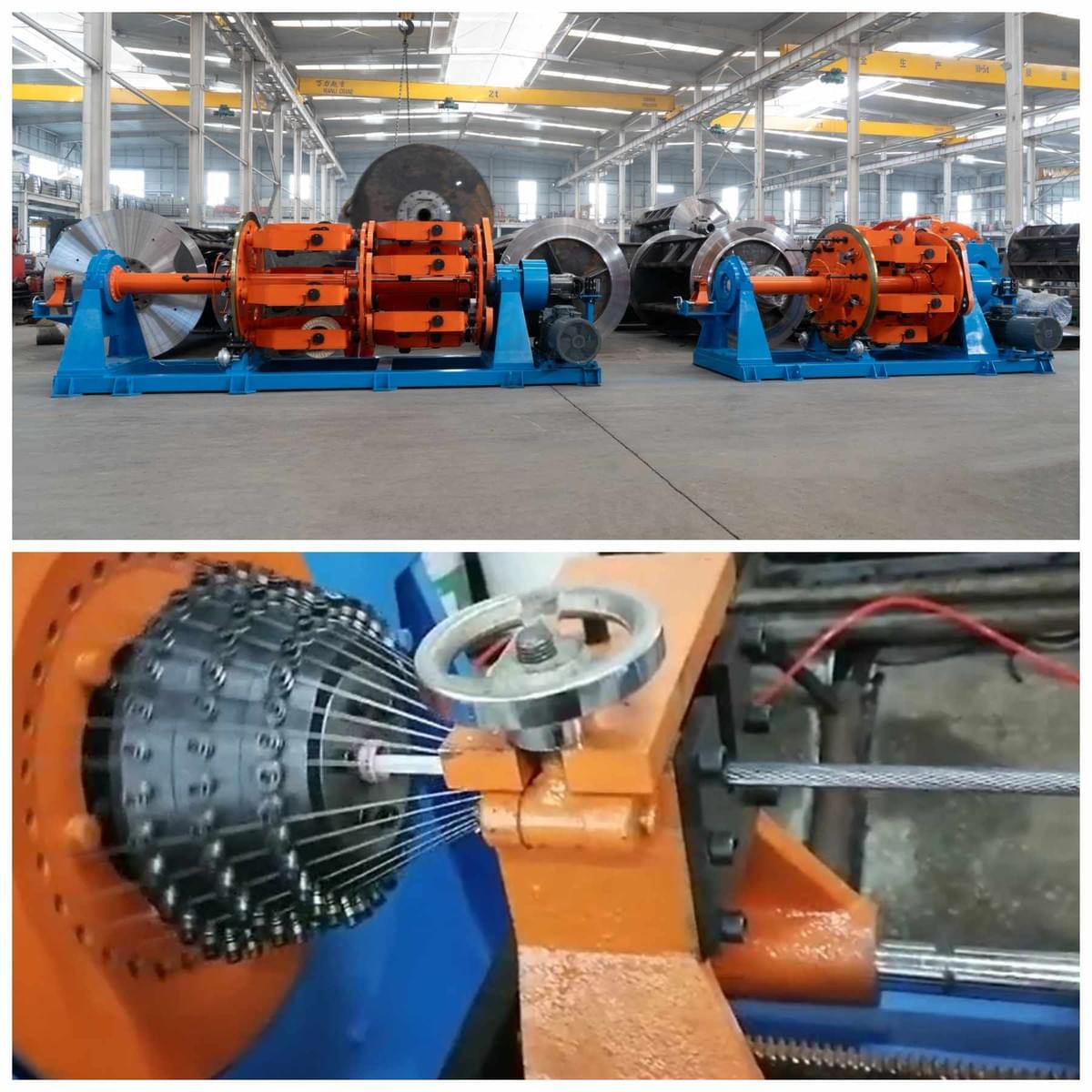
Step 3: Final Assembly
The stranded conductors are compacted to ensure tightness.
A corrosion-resistant coating (e.g., grease or polymer) is applied.
Markings & labeling are printed for identification.
Step 4: Quality Testing
Before delivery, OPGW undergoes:
Optical Testing (attenuation, bandwidth, continuity).
Mechanical Testing (tensile strength, bending, crush resistance).
Electrical Testing (DC resistance, short-circuit current capacity).
Conclusion
OPGW cable equipment can be selected from Planetary stranding machines or "tubular stranding machines", and the appropriate equipment should be selected according to the number of conductors.
Check video of OPGW cable manufacture process: